Facchinetti Srl – Innovation and Safety in Cheese Processing
Introduction
In the current scenario of the food industry, regulatory and technological evolution requires the implementation of increasingly sophisticated safety systems. The goal is twofold: to ensure maximum protection for operators and to optimize the efficiency of production processes. This is the context for the virtuous collaboration between Facchinetti Srl, an Italian company specializing in the design of cheese processing machinery, AutomationPlus, a system integrator with more than 30 years of experience at Facchinetti’s side, and ReeR Safety, a point of reference in the field of industrial safety.
This document delves into the solutions adopted for the PR01 machine, a cheese cutting and portioning machine, analyzing its operation, regulatory requirements and the safety solutions provided by ReeR to ensure efficient operation in full compliance with regulations.
Facchinetti Srl: Italian Excellence in Food Mechanization
With more than half a century of experience, Facchinetti Srl represents a well-established reality in the field of mechanization for cheese processing. Founded by Teresiano Facchinetti, the company initially focused its production on machinery for salting and perforating Gorgonzola, and then gradually expanded the range with solutions dedicated to cutting, brushing and packaging different varieties of cheese.
Present in key markets such as the United States, Brazil and France, Facchinetti is synonymous with reliability, precision and safety. Characteristics that make it an ideal partner for dairies and distributors who want to optimize their production processes while minimizing waste and increasing yield.
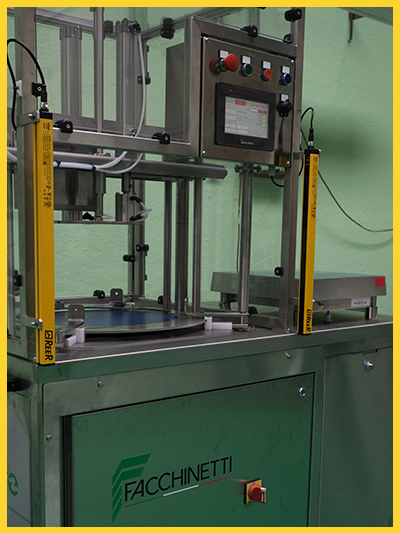
PR01: Advanced Automation for Cheese Portioning
The PR01 machine is the technological answer to the need for efficient and flexible automation of the portioning process for hard and soft cheeses. Designed to achieve productivity of up to 50 portions per minute, the PR01 is distinguished by its ability to offer three customizable cutting modes:
- by number of slices;
- by average weight;
- according to a predefined fixed weight.
The system is operated through an intuitive and functional user interface, which allows the operator to weigh the cheese via a dedicated scale, select the cutting mode from the front touchscreen, and start the cycle under the safest conditions.
Once the cheese is placed on the rotary table, the operating heart of the machine, the system automatically performs product centering and proceeds with cutting, achieved through a precise combination of controlled blade movement and synchronous table rotation, thus ensuring uniformity and quality of the result.
Given the level of automation and the presence of fast-moving components, the implementation of safety systems complying with current regulations was a must. In particular, PR01 is designed in accordance with the Machinery Directive 2006/42/EC and the ISO 13849 standard on functional safety of control systems.
The operating area of the rotary table is protected on three sides by fixed and movable guards. The movable guard is equipped with an electric safety lock, which prevents it from being opened during operation, allowing access only once a complete stop of all electrical and pneumatic movements is guaranteed. In addition, the presence of an emergency stop button (e-stop) allows the cycle to be stopped immediately if necessary.
For the fourth side of the operating area, dedicated to the loading of cheese on the table, and for the integrated management of the safety devices and functional elements of the PR01, Facchinetti Srl, in collaboration with its partner AutomationPlus, focused on a solution capable of combining regulatory compliance, maximum operator protection, operational continuity and minimization of machine downtime.
The decision to rely on ReeR Safety proved decisive: thanks to the technical support provided and the wide range of state-of-the-art devices, it was possible to implement a tailor-made safety system, perfectly integrated with PR01’s operational logic, without compromising its efficiency or productivity
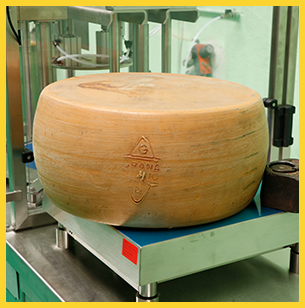
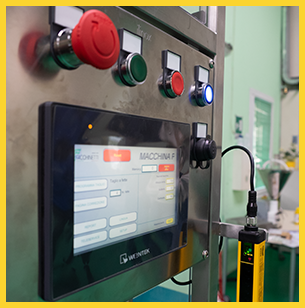
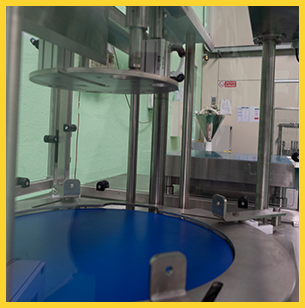
ReeR Safety Solutions: Intelligent Protection in the Service of Productivity
EOS4 Safety Barriers – Model EOS4 453 X
The EOS4 453 X optical safety barrier was adopted to protect the cheese entry area immediately before the cutting area. Characterized by:
- Type 4, SIL 3, PL e, Cat.4
- Controlled height: 450 mm
- 23 detection beams
This barrier fully meets the safety requirements of the regulations, ensuring constant control of the hazardous area. In case of beam interruption – caused, for example, by the passage of a limb or a foreign object – the machine immediately enters stop mode, preventing any potential accident. The selected model is equipped with automatic reset, a feature that enables rapid resumption of operations and helps reduce downtime.
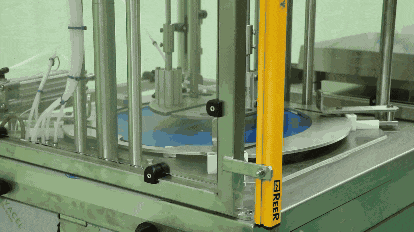
ReeR Solution
Â
EOS4 safety light curtainsÂ
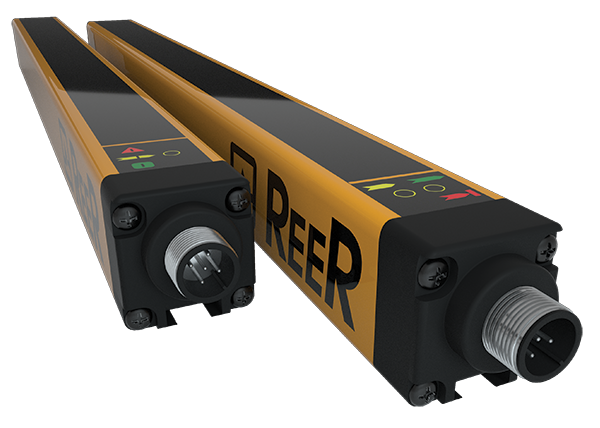
Hand Detection Safety Light Curtain with Automatic/Manual Restart and EDM
- Safety Level: Type 4 – PL e
- Resolution: 30 mm
- Protected height: 460 mm
- Max range: 12 m
MOSAIC M1 Safety Controller
The MOSAIC M1 safety controller is the heart of the entire safety system installed on PR01.
With the presence of 8 digital inputs and 2 pairs of OSSD outputs, the MOSAIC M1 receives signals from EOS4, the electric lock of the movable guard, and the e-stop button. The entire system is configurable via the dedicated MSD (Mosaic Safety Designer) software, which enables simple and intuitive logic design and operation.
Placed inside the machine’s electrical panel, the controller handles all safety logic, allowing for reduced wiring, cleaner electrical layout and modular configuration.
AutomationPlus, on the strength of its historical link with Facchinetti Srl, has chosen to use MOSAIC M1 as a central element in the design of the electrical panels of all machines, enhancing its reliability, programmability and expandability according to the complexity found.
MOSAIC MR4 Expansion Relay Module
For the management of the pneumatic actuators of the PR01 machine – particularly the pressure switches that control blade movement and other components – the MR4 Expansion Relay Module has been integrated with the MOSAIC M1 central unit, allowing four relay outputs to be added to the system.
In this way, the MR4 module is able to fully manage the absorption generated by the pneumatic valves, leaving the M1 central module to receive and evaluate feedback signals, thus ensuring that operating conditions meet safety standards before enabling the pneumatic devices to be activated.
This configuration ensures that the machine cannot operate under unsafe pressures, thereby preventing malfunctions and reducing the risk of accidents.
ReeR Solution
Â
Safety Controllers
Mosaic is a safety hub able to manage all safety functions of machinery. Configurable and scalable, provides cost reductions and minimal wiring.
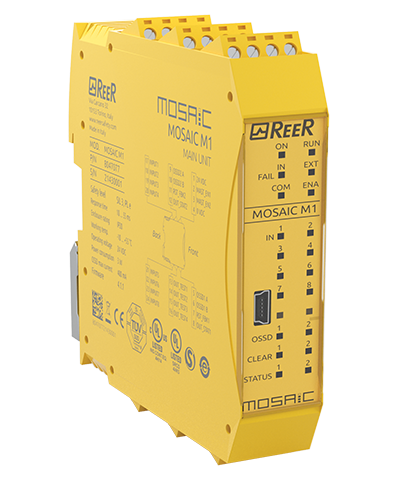
MOSAIC M1
Master Unit for the control of any other expansion unit, can also work as Stand-Alone.
- 8 digital inputs
- 2 OSSD pairs safety outputs
(PNP 400 mA) - 2 status outputs (PNP 100 mA)
- 4 test outputs
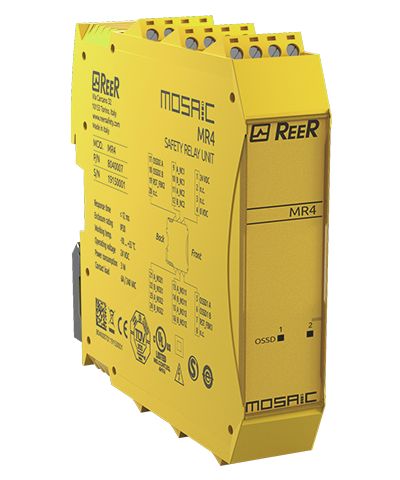
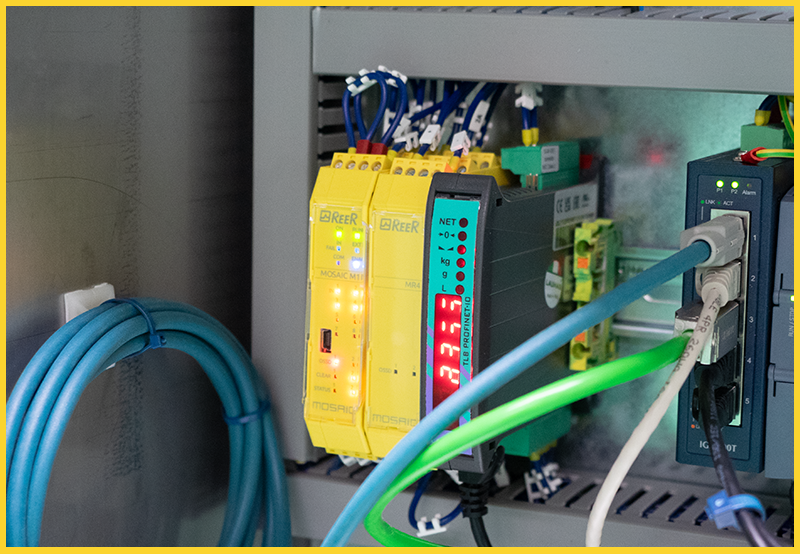
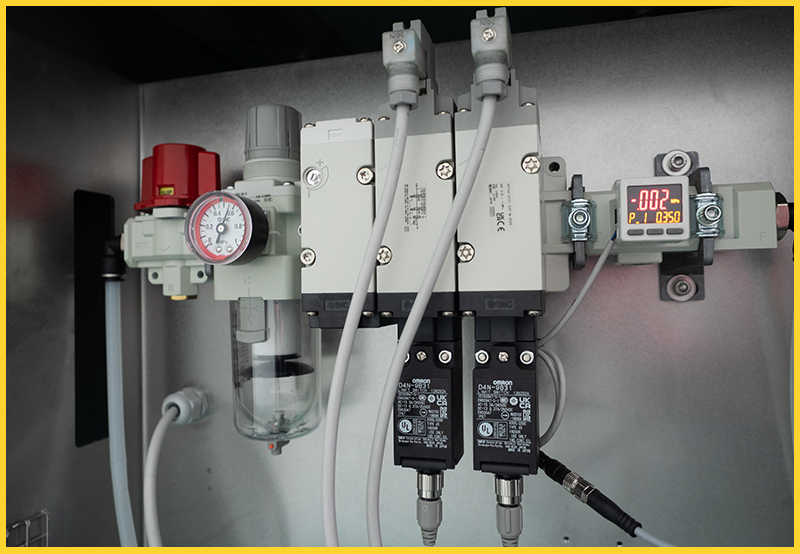
A unified platform for safety and control
Thanks to the combination of the MOSAIC M1 controller, the MR4 expansion module and the MSD configuration software, it was possible to centralize on a single integrated platform not only the management of safety logic, but also the direct control of the operating conditions of the pneumatic circuit.
This approach represents a distinctive element of the solution proposed by ReeR, resulting in a compact, efficient and easily reconfigurable system, perfectly in line with the needs for flexibility and operational continuity required in an industry such as the food industry.
Results of the Collaboration
The integration of ReeR’s safety solutions has brought important benefits to the entire production process:
- Certified Safety: full compliance with European regulations and drastic reduction of accident risk
- Operational Efficiency: reduced downtime thanks to automatic recovery and advanced safety logic
- Total Customization: modular system and software that can be configured according to specific production needs
- Unified Management: integrated platform for both operational and safety management
Conclusions
The case of Facchinetti Srl shows how the integration of advanced safety solutions can be a real competitive advantage. The synergy with AutomationPlus and ReeR Safety has enabled the creation of a state-of-the-art production system, where automation and operator protection coexist in a perfect balance.
The PR01 is not only an efficient machine, it is also a concrete example of industrial best practice, where safety technologies are not just a regulatory requirement, but a lever to improve quality, business continuity and end customer confidence.
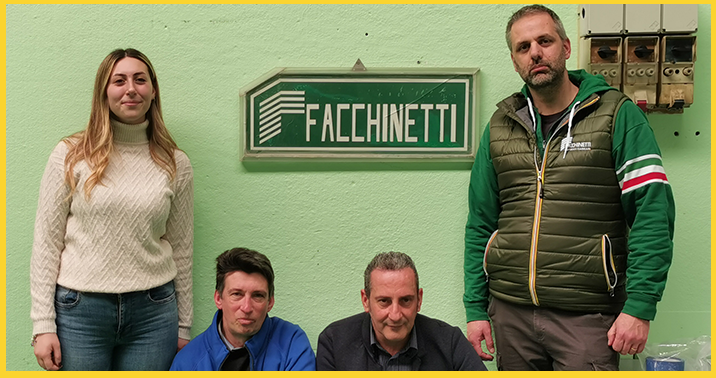
ReeR Safety: Safety in the Service of Industrial Excellence
ReeR Safety continues to develop solutions to ensure increasingly safe, high-performing and sustainable work environments. Our collaboration with leading companies in various sectors, such as Facchinetti Srl, testifies to our commitment to providing reliable, state-of-the-art technologies capable of making a difference in the most demanding manufacturing environments.
Contact us to discover all the solutions available.
ReeR, your future’s safe!