Sicurezza Intelligente per la Linea Automatizzata di Produzione Corpi Termostato
Una collaborazione vincente tra DeD Automation e ReeR Safety
Chi è DeD Automation
DeD Automation è un system integrator italiano specializzato nella progettazione e realizzazione di macchine speciali per l’automazione industriale. Con una forte esperienza nei settori più esigenti, in particolare l’automotive, l’azienda si è affermata come partner strategico per clienti che necessitano di impianti per il collaudo, assemblaggio, imballaggio e test di componenti medio-piccoli.
L’approccio di DeD si distingue per l’attenzione alle esigenze specifiche del cliente, a partire dall’ascolto e dall’analisi preliminare dell’oggetto da automatizzare. Ogni progetto viene sviluppato internamente: dalla progettazione meccanica in 3D allo sviluppo elettrico, hardware, software e, elemento centrale, la sicurezza funzionale. La filosofia progettuale di DeD prevede che la sicurezza non sia un’aggiunta finale, bensì parte integrante del concept iniziale dell’impianto.
Il Cliente e la Sfida
Per un’importante realtà produttiva con la quale collabora da oltre vent’anni, operante nel settore automotive e specializzata nella realizzazione di corpi termostato, DeD ha progettato e messo in funzione, nel 2022, una nuova linea automatizzata avanzata. Il cliente aveva l’obiettivo di aumentare l’efficienza produttiva, mantenendo elevati standard di qualità e integrando un sistema di sicurezza capace di garantire continuità operativa anche in caso di interventi localizzati.
La sfida principale era realizzare una linea moderna e performante, dotata di sistemi di sicurezza modulari e intelligenti, in grado di gestire la complessità del processo senza compromettere la produttività.
La Linea di Produzione: Struttura e Funzionamento
La linea sviluppata da DeD si estende per circa 14 metri ed è composta da 16 stazioni operative suddivise in cinque macro-zone funzionali. Il ciclo produttivo è completamente automatizzato, ma richiede la presenza dell’operatore in due fasi strategiche: il carico iniziale e lo scarico finale del prodotto buono. Il tempo ciclo medio per ogni pezzo è di circa 35 secondi.
Zona 1 – Carico Iniziale e Pre-Assemblaggio: L’operatore carica manualmente i componenti all’interno di una saldatrice a rotofrizione. Dopo l’aggiunta della guarnizione, il pezzo viene collocato su un pallet che dà inizio al suo avanzamento lungo la linea. L’area è protetta da una barriera immateriale e da ripari mobili interbloccati, che permettono un intervento sicuro in caso di necessità;
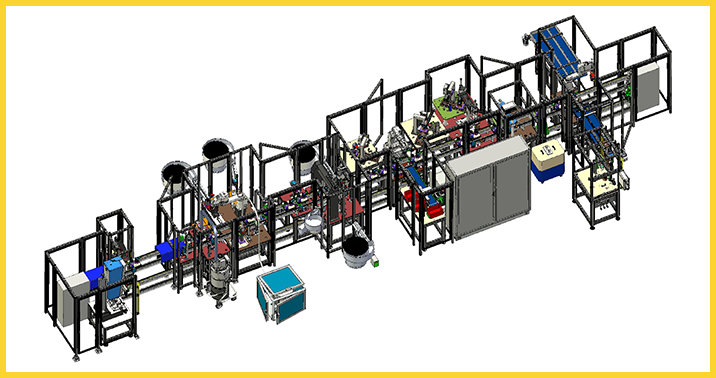
Zona 2 – Assemblaggio Automatico: Qui avviene il montaggio automatico di vari componenti come molle, traversini, bulbi, guarnizioni, sensori e forcelle, alimentati tramite vibratori. Il controllo qualità è integrato nel processo. L’eventuale inceppamento di un componente non ferma l’intera linea, ma solo la porzione interessata, garantendo continuità al ciclo produttivo;
Zona 3 – Collaudo e Marcatura: In questa fase vengono effettuati test di tenuta pneumatica, tenuta elettrica, verifica della continuità e controllo di eventuali trafilamenti. I componenti conformi sono marcati con laser per garantirne la tracciabilità;
Zona 4 – Smistamento:Il sistema esegue la selezione automatica tra componenti conformi e quelli scartati, con possibilità di categorizzare il motivo dello scarto (difetti elettrici, montaggio errato, errori di collaudo, ecc.);
Zona 5 – Controllo Finale e Imballaggio: L’operatore effettua un controllo finale, legge il Data Matrix, verifica la presenza di tutti i componenti previsti e applica i tappi protettivi. I prodotti sono così pronti per la spedizione.
Ogni zona è progettata per operare in modo autonomo: in caso di malfunzionamento o necessità di manutenzione in un punto specifico, è possibile arrestare solo la zona interessata, senza compromettere l’intero processo. Ognuna di queste è servita da un’UTA (unità trattamento aria) che fornisce energia pneumatica alle stazioni di lavoro. Tutte le UTA locali sono gestite da una UTA centrale posizionata nel quadro generale che filtra e distribuisce aria a 6 bar in modo costante.
Per le necessità manifestate dal cliente ed esposte nel prossimo paragrafo, è importante sottolineare che ciascuna stazione è protetta dai seguenti dispositivi di sicurezza:
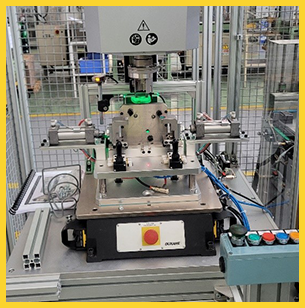
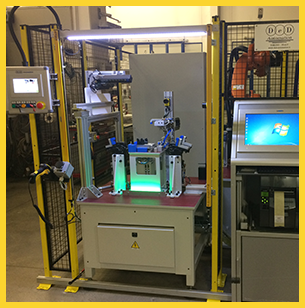
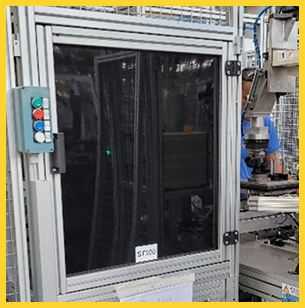
- E-stop: ha lo scopo di determinare l’arresto della macchina (arresto in categoria 0) e il sezionamento dell’energia pneumatica. Richiede intervento dell’operatore per il ripristino;
- Ripari fissi: impediscono l’accesso agli elementi mobili durante il normale funzionamento e quelli a cui l’accesso è occasionale per le sole operazioni manutentive. Sono fissati alla struttura della macchina mediante viti che richiedono l’utilizzo di utensili per lo smontaggio;
- Ripari mobili interbloccati: fissati mediante cerniere e provvisti di maniglie per facilitarne l’apertura. Sono associati a microinterruttori elettromagnetici che ne impediscono l’apertura quando la macchina è in marcia;
- Barriere fotoelettriche di sicurezza: proteggono le zone pericolose creando una barriera immateriale che si attiva all’avvio del ciclo di lavorazione e, se intercettate dall’operatore, fermano immediatamente gli elementi mobili della macchina.
Questa architettura permette una gestione selettiva e sicura delle operazioni di fermo e ripristino.
Le Esigenze di Sicurezza
Data la complessità e modularità della linea, DeD ha definito con precisione i requisiti di sicurezza:
- Gestione indipendente delle cinque zone, senza arresti totali in caso di interventi localizzati
- Controllo puntuale di tutti i dispositivi di sicurezza, inclusi pulsanti di emergenza, microinterruttori, interblocchi, barriere fotoelettriche di sicurezza
- Sezionamento pneumatico ed elettrico intelligente per ciascuna zona, incluso il controllo degli assi elettrici
- Espandibilità futura, con I/O di sicurezza già predisposti per nuove postazioni
- Ottimizzazione dei cablaggi e semplificazione della programmazione attraverso una piattaforma di sicurezza centralizzata
Per ogni zona sono necessari non meno di:
- 4 ingressi di sicurezza dedicati
- Uscite per la gestione di STO, barriere e ripari
- Moduli di raccolta segnali locali e diagnostica
- Uscite dedicate alla gestione dei robot nelle zone 1 e 2
La Soluzione ReeR: Sistema di Sicurezza Modulare MOSAIC
La piattaforma modulare MOSAIC di ReeR Safety si è dimostrata la soluzione ideale per soddisfare le esigenze di sicurezza del progetto. Al centro dell’architettura di sicurezza è stato integrato il modulo M1S COM, dotato di:
- 8 ingressi digitali
- 4 uscite OSSD (2 coppie)
- 4 uscite di test
- 2 porte RJ45 per comunicazione con i principali bus di campo (EtherCAT, PROFINET, Modbus TCP, Ethernet IP)
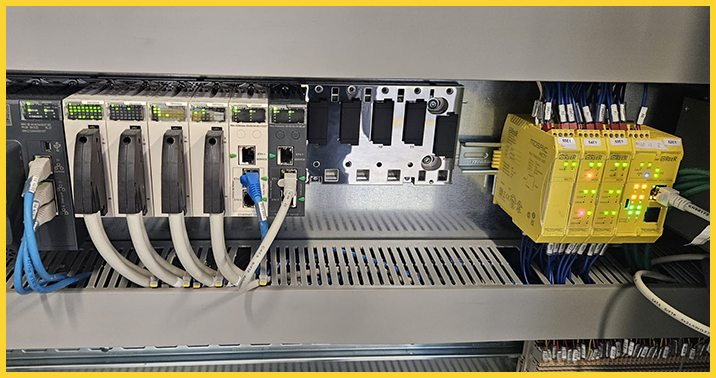
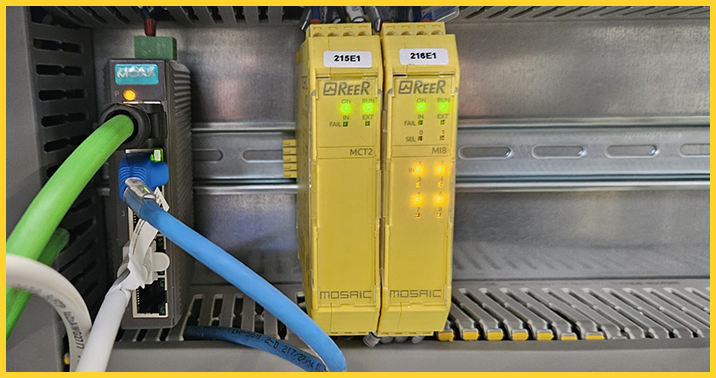
Additional Modules for a Distributed Control
MI16 e MI8: for collecting safety signals (emergency buttons, barriers, interlocks);
MO4: for managing OSSD outputs to actuators, valves or disconnect switches;
MCT1 e MCT2: for remote communication with local boxes via MSC bus.
Questa configurazione consente la gestione sicura e indipendente di ciascuna zona. Ogni unità locale comunica con il modulo centrale, consentendo l’arresto selettivo delle singole aree e una diagnostica puntuale. In caso di intervento, gli operatori possono operare in totale sicurezza senza compromettere l’intera line.
Soluzione ReeR
Controllori e interfacce di sicurezza
Mosaic è un sistema di sicurezza in grado di gestire tutte le funzioni di sicurezza di un macchinario o di un gruppo di macchinari. Configurabile ed espandibile, permette la riduzione dei costi e un cablaggio più semplice.
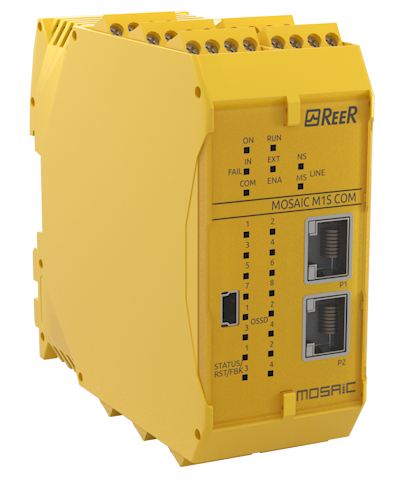
MOSAIC M1S COM
Modulo principale, utilizzabile anche in modalità “Stand-Alone”, in grado di controllare gli altri moduli addizionali di espansione.
- 8 ingressi digitali
- Fino a 4 ingressi per interblocco del riavvio e EDM
- 4 uscite di sicurezza OSSD singole, oppure 2 coppie (PNP 400 mA)
- Fino a 4 uscite di status (PNP 100 mA)
- 4 uscite di test (per il monitoraggio dei corto circuiti)
- Interfaccia field-bus Integrata. Protocolli: Ethernet IP, EtherCAT, PROFINET, Modbus TCP
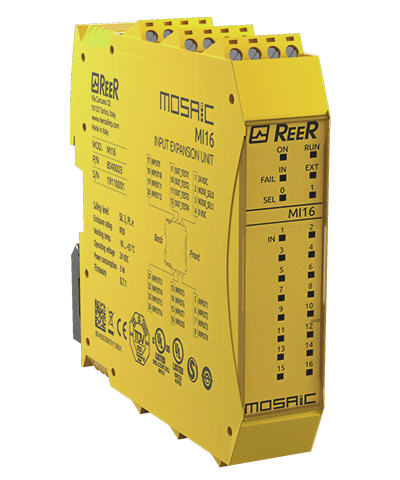
MOSAIC MI8 – MI16
Modulo di espansione ingressi.
- MI8: 8 ingressi digitali 4 uscite di test
- MI16: 16 ingressi digitali 4 uscite di test
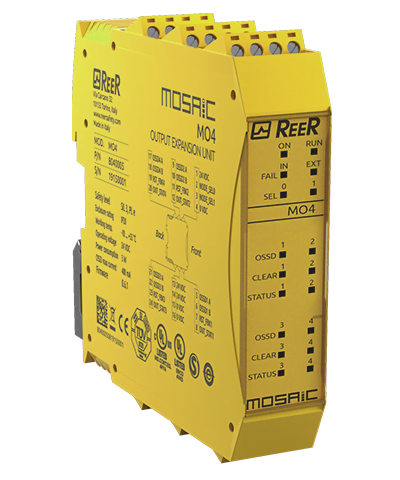
MOSAIC MO4
Modulo di espansione uscite di sicurezza.
- 4 coppie di uscite di sicurezza OSSD
- 4 ingressi per interblocco del riavvio e EDM
- 4 uscite di status
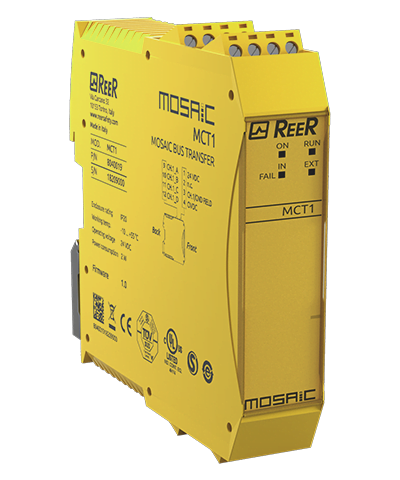
MOSAIC MCT1 – MCT2
Modulo d’interfaccia, consente il collegamento di espansioni remote al modulo principale tramite il bus MSC.
- MCT1: 1 connettore d’interfaccia (1 I/O)
- MCT2: 2 connettori d’interfaccia (2 I/O)
Benefici ottenuti
L’adozione della piattaforma MOSAIC ha portato benefici concreti e misurabili:
- Modularità e scalabilità: possibilità di espandere facilmente la linea con nuove stazioni o sensori;
- Riduzione dei tempi di cablaggio e installazione: grazie alla struttura decentralizzata;
- Gestione distribuita della sicurezza: ogni zona lavora in modo autonomo;
- Diagnostica avanzata e manutenzione semplificata con il software gratuito MSD, che consente anche la simulazione e validazione del progetto;
- Alta disponibilità dell’impianto: i fermi macchina sono localizzati e minimizzati;
- Standardizzazione e semplificazione: uniformità dei componenti e maggiore efficienza nella gestione del magazzino ricambi.
Una Partnership Solida per un’Automazione Sicura
Questo progetto rappresenta un esempio virtuoso di come la sinergia tra un integratore esperto come DeD Automation e un fornitore leader di soluzioni di sicurezza come ReeR possa generare impianti sicuri, efficienti e pronti per le sfide future.
La fiducia che lega le due aziende è il risultato di anni di collaborazione e successi condivisi. Il sistema MOSAIC è già stato utilizzato in numerose applicazioni, dai banchi semplici scegliendolo come soluzione stand-alone alle linee automatizzate più complesse come quella appena descritta per la realizzazione dei corpi termostato. La sua flessibilità e affidabilità lo rendono la scelta naturale per ogni contesto produttivo che richiede sicurezza senza compromessi.
If you too are designing an automated line and would like to integrate smart, flexible and scalable safety solutions, contact the ReeR experts.
Siamo pronti ad accompagnarti verso una nuova era dell’automazione sicura.
ReeR, your future’s safe!