Category B
Fault tolerance = 0
- PLmax = b
- DC = 0
- MTTFD = from low to medium
- Use of basic safety principles (components must withstand the expected
operating stresses)
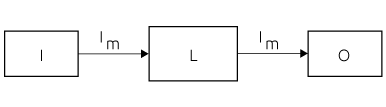
Single channel without diagnostic
The categories reflect what is already happening in the industrial machinery world. Most of the controls implemented can be reduced to a limited number of safety control types. That means:
NOTE: The lines and arrows in the following figures represent logical, functional, and diagnostic interconnections.
Fault tolerance = 0
Single channel without diagnostic
Fault tolerance = 0
Single channel without diagnostic
NOTE: A “well tried component” is a component that has been:
Widely used in the past with positive results in similar applications
Built and verified using principles that demonstrate its suitability, reliability and robustness for safety related applications
The qualification of a component as well tried depends on its application. Example, a position switch with open contacts can be well tested for a machine tool and at the same time inappropriate for application in the food industry.
Fault tolerance = 0
Single channel with diagnostic
The test must not create a dangerous situation (e.g increase in the response time).
The safety function must be tested at least during the start-up and before a dangerous condition can occur (starting a new cycle). The frequency of the functional channel test had to be at least 100 times higher than the request rate of the safety function.
For ratios greater than 25 and less than 100 it is possible to use the PFHD values (shown in table K .1 for Cat. 2) multiplied by a factor of 1.1.
The test can also be performed at the same time as the safety function request, but the overall time to detect the fault and to bring the machine to a safe condition (usually the machine is stopped) must be shorter than the time taken by a person to reach the dangerous point.
For PLr = a and up to PLr = c, when, upon detection of the fault, it is not possible to initiate a safe state (for example due to the welding of the contact in the output device), it may be sufficient that the output OTE only provides a warning signal.
For PL r = d, the OTE output must initiate a safe state which is maintained until the fault is cleared.
Fault tolerance = 1
A single fault does not lead to the loss of the safety function.
When reasonably practicable, the single fault must be detected during or before the next safety function request.
Not all faults can be detected. The accumulation of undetected faults leads to the loss of the safety function.
Dual channel with diagnostic
Fault tolerance = 1
A single fault does not lead to the loss of the safety function.
Faults must be detected in time before the loss of safety function. For example, immediately upon their occurrence, or when the machine is turned on, or at the end of the operating cycle. If this detection is not possible, the combination of two faults must not lead to the loss of the safety function.
Dual channel with diagnostic