Seguridad inteligente para la línea de producción automatizada de carcasas de termostato
Una colaboración ganadora entre DeD Automation y ReeR Safety
Acerca de DeD Automation
DeD Automation es un integrador de sistemas italiano especializado en el diseño y la fabricación de máquinas especiales para la automatización industrial. Con una sólida experiencia en los sectores más exigentes, en particular la automoción, la empresa se ha consolidado como un socio estratégico para los clientes que necesitan sistemas para el ensayo, el ensamblaje, el embalaje y la comprobación de componentes pequeños y medianos. El enfoque de DeD se distingue por su atención a las necesidades específicas del cliente, empezando por la escucha y el análisis preliminar del objeto que se desea automatizar. Cada proyecto se desarrolla internamente: desde el diseño mecánico en 3D hasta el desarrollo eléctrico, pasando por el hardware, el software y, elemento central, la seguridad funcional. La filosofía de diseño de DeD es que la seguridad no es un añadido final, sino parte integrante del concepto inicial del sistema.
El enfoque de DeD se distingue por su atención a las necesidades específicas del cliente, empezando por la escucha y el análisis preliminar del objeto que se va a automatizar. Cada proyecto se desarrolla internamente: desde el diseño mecánico en 3D hasta el desarrollo eléctrico, el hardware, el software y, elemento central, la seguridad funcional. La filosofía de diseño de DeD es que la seguridad no es un añadido final, sino parte integrante del concepto inicial del sistema.
El cliente y el reto
Para una importante empresa manufacturera con la que trabaja desde hace más de 20 años, que opera en el sector de la automoción y está especializada en la fabricación de carcasas de termostatos, DeD diseñó y puso en marcha en 2022 una nueva línea automatizada avanzada. El objetivo del cliente era aumentar la eficiencia de la producción manteniendo altos estándares de calidad e integrando un sistema de seguridad capaz de garantizar la continuidad operativa incluso en caso de intervenciones localizadas.
El principal reto era crear una línea moderna y de alto rendimiento equipada con sistemas de seguridad modulares e inteligentes que pudieran gestionar la complejidad del proceso sin comprometer la productividad.
La línea de producción: Estructura y funcionamiento
La línea desarrollada por DeD tiene una extensión de unos 14 metros y consta de 16 estaciones operativas divididas en cinco macrozonas funcionales. El ciclo de producción está totalmente automatizado, pero requiere la presencia del operario en dos fases estratégicas: la carga inicial y la descarga final del producto bueno. La duración media del ciclo para cada pieza es de unos 35 segundos.
Zona 1 – Carga inicial y premontaje: El operario carga manualmente los componentes dentro de una soldadora de rotofricción. Una vez añadida la junta, la pieza se coloca en un palé que inicia su avance por la línea. La zona está protegida por una barrera intangible y resguardos móviles enclavados, que permiten intervenir con seguridad en caso necesario;El cliente y el reto;
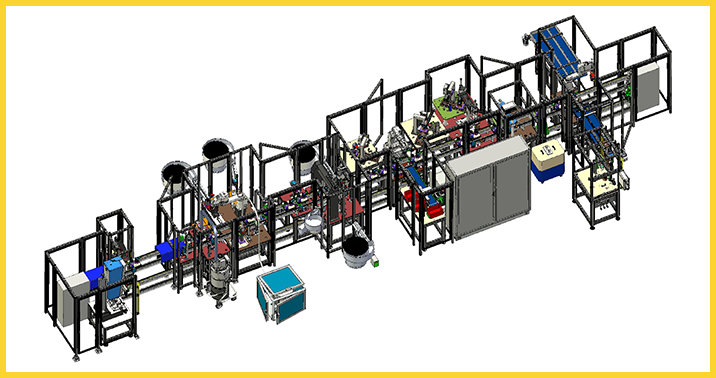
Zona 2 – Montaje automático: Aquí tiene lugar el montaje automático de diversos componentes, como muelles, traviesas, bombillas, juntas, sensores y horquillas, alimentados mediante vibradores. El control de calidad está integrado en el proceso. Cualquier atasco de un componente no detiene toda la línea, sino sólo la parte afectada, lo que garantiza la continuidad del ciclo de producción;
Zona 3 – Pruebas y marcado: En esta fase se llevan a cabo la estanqueidad neumática, la estanqueidad eléctrica, la comprobación de continuidad y la comprobación de fugas. Los componentes conformes se marcan con láser para garantizar su trazabilidad;
Zona 4 – Clasificación: El sistema realiza una clasificación automática entre componentes conformes y rechazados, con la posibilidad de categorizar el motivo del rechazo (defectos eléctricos, montaje incorrecto, errores de prueba, etc);
Zona 5 – Comprobación final y embalaje: El operario realiza una comprobación final, lee la matriz de datos, verifica la presencia de todos los componentes previstos y aplica tapas protectoras. A continuación, los productos están listos para su envío.
Cada zona está diseñada para funcionar de forma independiente: en caso de avería o necesidad de mantenimiento en un punto concreto, sólo puede detenerse la zona afectada, sin que ello afecte a todo el proceso. Cada una de ellas está servida por una UTA (unidad de tratamiento de aire) que suministra energía neumática a los puestos de trabajo. Todas las UTA locales están gestionadas por una UTA central situada en el cuadro principal que filtra y distribuye aire a 6 bares de forma constante.
Para las necesidades expresadas por el cliente y expuestas en el apartado siguiente, es importante señalar que cada estación está protegida por los siguientes dispositivos de seguridad:
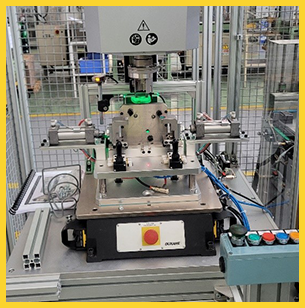
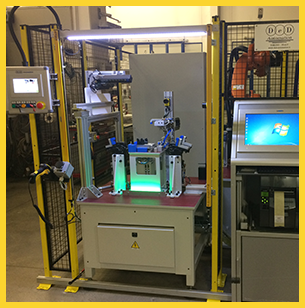
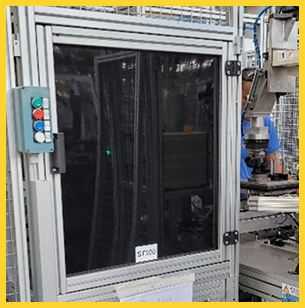
- E-stop: tiene por objeto determinar la parada de la máquina (parada en categoría 0) y la desconexión de la alimentación neumática. Requiere la intervención del operador para su rearme;
- Resguardos fijos: impiden el acceso a los elementos móviles durante el funcionamiento normal y a aquellos cuyo acceso es ocasional sólo para operaciones de mantenimiento. Se fijan a la estructura de la máquina mediante tornillos que requieren el uso de herramientas para su desmontaje;
- Resguardos móviles con enclavamiento: fijados mediante bisagras y provistos de asas para facilitar su apertura. Están asociados a microinterruptores electromagnéticos que impiden su apertura cuando la máquina está en marcha;
- Cortinas ópticas de seguridad: protegen las zonas peligrosas creando una barrera intangible que se activa al iniciarse el ciclo de mecanizado y, si es interceptada por el operario, detiene inmediatamente los elementos móviles de la máquina.
Esta arquitectura permite una gestión selectiva y segura de las operaciones de parada y recuperación.
Las necesidades de seguridad
Debido a la complejidad y modularidad de la línea, DeD ha definido con precisión los requisitos de seguridad:
- Gestión independiente de las cinco zonas, sin paradas totales en caso de intervenciones localizadas;
- Control puntual de todos los dispositivos de seguridad, incluidos pulsadores de emergencia, microinterruptores, enclavamientos, cortinas ópticas de seguridad;
- Seccionamiento neumático y eléctrico inteligente para cada zona, incluido el control eléctrico de ejes;
- Ampliabilidad futura, con E/S de seguridad ya preparadas para nuevas ubicaciones;
- Optimización del cableado y simplificación de la programación mediante una plataforma de seguridad centralizada.
Cada zona requiere como mínimo:
- 4 entradas de seguridad dedicadas
- Salidas para la gestión de STO, barreras y resguardos
- Módulos para la recogida local de señales y diagnósticos
- Salidas dedicadas a la gestión de robots en las zonas 1 y 2
La solución de ReeR: Sistema modular de seguridad MOSAIC
La plataforma modular MOSAIC de ReeR Safety demostró ser la solución ideal para satisfacer las necesidades de seguridad del proyecto. En el núcleo de la arquitectura de seguridad se encuentra el módulo MOSAIC M1S COM, equipado con:
- 8 entradas digitales
- Salidas OSSD (2 pares)
- 4 salidas de prueba
- 2 puertos RJ45 para comunicación con los principales buses de campo (EtherCAT, PROFINET, Modbus TCP, Ethernet IP)
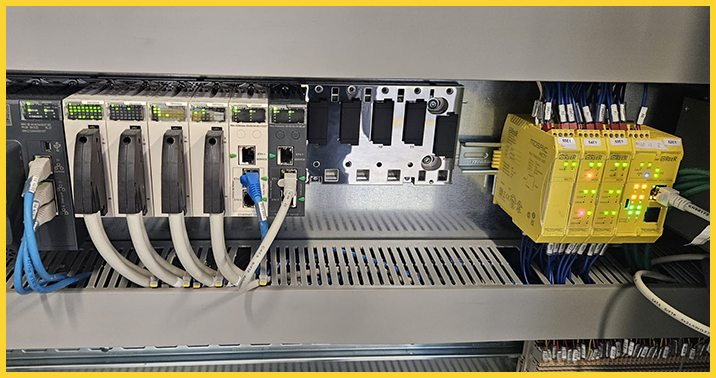
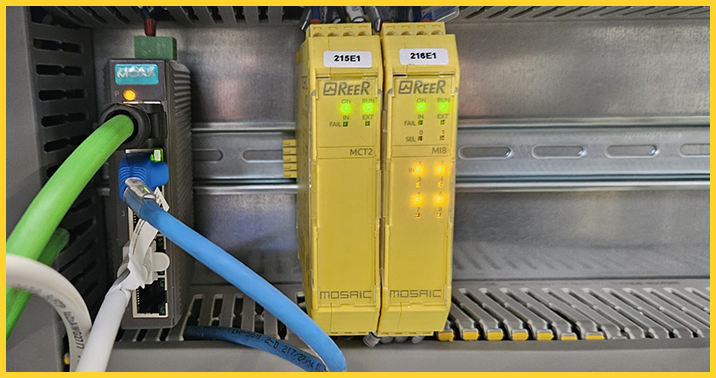
Módulos adicionales para un control distribuido
MI16 y MI8: para la recogida de señales de seguridad (pulsadores de emergencia, barreras, enclavamientos);
MO4: para la recogida de señales de seguridad (pulsadores de emergencia, barreras, enclavamientos);
MCT1 y MCT2: para la comunicación remota con las cajas locales a través del bus MSC.
Esta configuración permite una gestión segura e independiente de cada zona. Cada unidad local se comunica con el módulo central, lo que permite el apagado selectivo de zonas individuales y el diagnóstico oportuno. En caso de intervención, los operadores pueden operar con seguridad sin comprometer toda la línea.
Solución ReeR
Controladores e interfaces de seguridad
Mosaic es un concentrador de seguridad capaz de gestionar todas las funciones de seguridad de la maquinaria. Configurable y escalable, permite reducir costes y minimizar el cableado
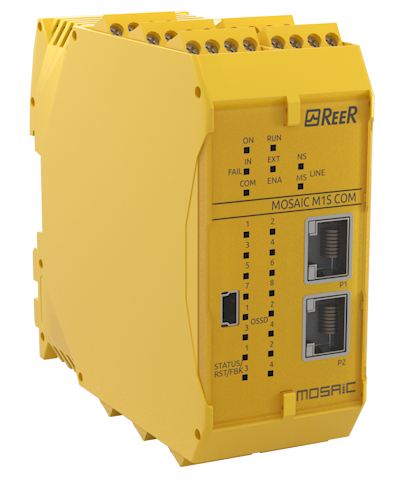
MOSAIC M1S COM
Unidad Maestra para el control de cualquier otra unidad de expansión, también puede funcionar como Stand-Alone.
- 8 entradas digitales
- 4 entradas para bloqueo de arranque/rearranque y EDM
- 4 sencillas OSSD o 2 pares (400 mA)
- 4 salidas de estado (PNP 100 mA)
- 4 salidas de prueba (para supervisión de cortocircuitos)
- Bus de campo integrado Inteface. Protocolos: Ethernet IP, EtherCAT, PROFINET, Modbus Solución TCP
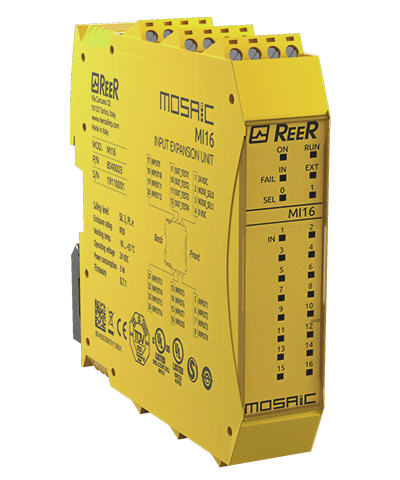
MOSAIC MI8 – MI16
Módulo de expansión de entrada
- MI8: 8 entradas digitales y 4 salidas de prueba
- MI16: 16 entradas digitales y 4 salidas de prueba
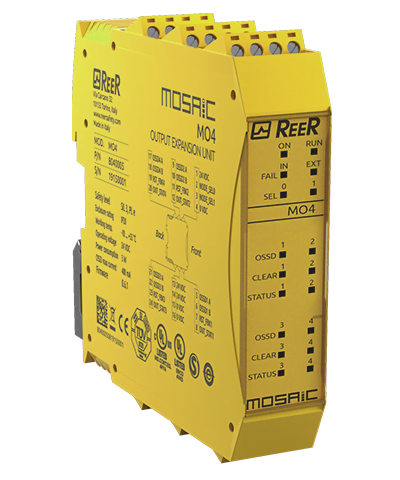
MOSAIC MO4
Unidad de expansión de salida
- 4 pares de salidas de seguridad OSSD
- 4 entradas para start/restart y control de relé externo (EDM)
- 4 salidas de estado
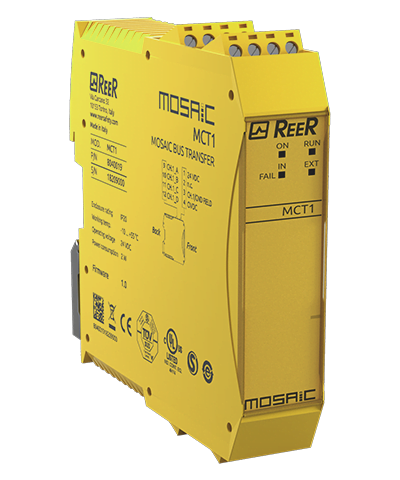
MOSAIC MCT1 – MCT2
Unidad de interfaz que permite la conexión de ampliaciones remotas a través del bus MSC
- MCT1: 1 interfaz de conexión (1 E/S)
- MCT2: Interfaz de 2 conexiones (2 E/S)
Beneficios obtenidos
La adopción de la plataforma MOSAIC ha aportado beneficios concretos y cuantificables:
- Modularidad y escalabilidad: capacidad para ampliar fácilmente la línea con nuevas estaciones o sensores;
- Reducción del cableado y del tiempo de instalación: gracias a la estructura descentralizada;
- Gestión de seguridad distribuida: cada zona funciona de forma autónoma;
- Diagnóstico avanzado y mantenimiento simplificado con el software gratuito MSD, que también permite la simulación y la validación del diseño;
- Alta disponibilidad de la planta: el tiempo de inactividad se localiza y minimiza;
- Estandarización y simplificación: uniformidad de los componentes y mayor eficiencia en la gestión del inventario de piezas de repuesto.
Una asociación sólida para una automatización segura
Este proyecto es un ejemplo virtuoso de cómo la sinergia entre un integrador experimentado como DeD Automation y un proveedor líder de soluciones de seguridad como ReeR puede generar instalaciones seguras, eficientes y preparadas para futuros retos.
La confianza que une a las dos empresas es el resultado de años de colaboración y éxitos compartidos. El sistema MOSAIC ya se ha utilizado en numerosas aplicaciones, desde simples contadores eligiéndolo como solución autónoma hasta líneas automatizadas más complejas como la que acabamos de describir para fabricar carcasas de termostatos. Su flexibilidad y fiabilidad lo convierten en la elección natural para cualquier contexto de producción que requiera una seguridad sin concesiones.
Si usted también está diseñando una línea automatizada y desea integrar soluciones de seguridad inteligentes, flexibles y escalables, póngase en contacto con los expertos de ReeR.
Estamos preparados para acompañarle en una nueva era de automatización segura.
ReeR, your future’s safe!