Intelligente Sicherheit für eine automatisierte Produktionslinie für Thermostatgehäuse
Eine gewinnbringende Zusammenarbeit zwischen DeD Automation und ReeR Safety
Über DeD Automation
DeD Automation ist ein italienischer Systemintegrator, der sich auf die Entwicklung und Herstellung von Sondermaschinen für die industrielle Automatisierung spezialisiert hat. Mit einer großen Erfahrung in den anspruchsvollsten Sektoren, insbesondere in der Automobilindustrie, hat sich das Unternehmen als strategischer Partner für Kunden etabliert, die Systeme für die Prüfung, Montage, Verpackung und den Test von kleinen bis mittelgroßen Komponenten benötigen. Die Herangehensweise von DeD zeichnet sich dadurch aus, dass sie auf die spezifischen Bedürfnisse des Kunden eingeht, beginnend mit dem Zuhören und der Voranalyse des zu automatisierenden Objekts. Jedes Projekt wird intern entwickelt: von der mechanischen 3D-Konstruktion über die elektrische Entwicklung, die Hardware, die Software und – als zentrales Element – die funktionale Sicherheit. Die Design-Philosophie von DeD sieht vor, dass die Sicherheit nicht ein nachträglicher Zusatz ist, sondern ein integraler Bestandteil der ursprünglichen Konzeption des Systems.
Die Herangehensweise von DeD zeichnet sich dadurch aus, dass sie auf die spezifischen Bedürfnisse des Kunden eingeht, beginnend mit dem Zuhören und der Voranalyse des zu automatisierenden Objekts. Jedes Projekt wird intern entwickelt: von der mechanischen 3D-Konstruktion über die elektrische Entwicklung, die Hardware, die Software und – als zentrales Element – die funktionale Sicherheit. Die Designphilosophie von DeD ist, dass die Sicherheit nicht ein nachträglicher Zusatz ist, sondern ein integraler Bestandteil des ursprünglichen Konzepts des Systems.
Der Kunde und die Herausforderung
Für ein großes Produktionsunternehmen, mit dem DeD seit mehr als 20 Jahren zusammenarbeitet und das in der Automobilbranche tätig und auf die Herstellung von Thermostatgehäusen spezialisiert ist, hat DeD im Jahr 2022 eine neue fortschrittliche automatisierte Linie konzipiert und in Betrieb genommen. Das Ziel des Kunden war es, die Produktionseffizienz zu steigern und gleichzeitig hohe Qualitätsstandards einzuhalten und ein Sicherheitssystem zu integrieren, das die Kontinuität des Betriebs auch im Falle von lokalen Eingriffen gewährleistet.
Die größte Herausforderung bestand darin, eine moderne, leistungsstarke Linie zu schaffen, die mit modularen, intelligenten Sicherheitssystemen ausgestattet ist, die die Komplexität des Prozesses bewältigen können, ohne die Produktivität zu beeinträchtigen.
Die Produktionslinie: Aufbau und Betrieb
Die von DeD entwickelte Linie ist etwa 14 Meter lang und besteht aus 16 Arbeitsstationen, die in fünf funktionelle Makrozonen unterteilt sind. Der Produktionszyklus ist vollständig automatisiert, erfordert jedoch die Anwesenheit des Bedieners in zwei strategischen Phasen: dem anfänglichen Beladen und dem endgültigen Entladen des Produkts. Die durchschnittliche Zykluszeit für jedes Teil beträgt etwa 35 Sekunden.
Zone 1 – Erstes Laden und Vormontage: Der Bediener lädt die Komponenten manuell in eine Rotationsschweißmaschine. Nach dem Hinzufügen der Dichtung wird das Teil auf eine Palette gelegt, die sich dann auf den Weg durch die Fertigungslinie macht. Der Bereich ist durch eine immaterielle Barriere und verriegelte, bewegliche Schutzvorrichtungen geschützt, die im Bedarfsfall ein sicheres Eingreifen ermöglichen;
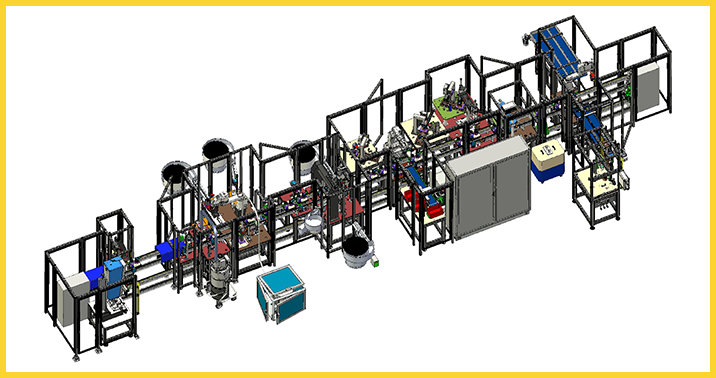
Zone 2 – Automatische Montage: Hier findet die automatische Montage verschiedener Komponenten wie Federn, Schwellen, Glühbirnen, Dichtungen, Sensoren und Gabeln statt, die über Rüttler zugeführt werden. Die Qualitätskontrolle ist in den Prozess integriert. Bei einer Verklemmung eines Bauteils wird nicht die gesamte Linie angehalten, sondern nur der betroffene Teil, so dass die Kontinuität des Produktionszyklus gewährleistet ist;
Zone 3 – Prüfung und Kennzeichnung: In dieser Phase werden die pneumatische und elektrische Dichtheit, die Durchgangsprüfung und die Dichtheitsprüfung durchgeführt. Die konformen Komponenten werden mit einer Lasermarkierung versehen, um die Rückverfolgbarkeit zu gewährleisten;
Zone 4 – Sortierung: Das System führt eine automatische Sortierung zwischen konformen und abgelehnten Bauteilen durch, mit der Möglichkeit, den Grund für die Ablehnung zu kategorisieren (elektrische Defekte, falsche Montage, Testfehler usw.);
Zone 5 – Endkontrolle und Verpacken: Der Bediener führt eine Endkontrolle durch, liest die Data Matrix, überprüft das Vorhandensein aller erwarteten Komponenten und bringt Schutzkappen an. Danach sind die Produkte versandfertig;
ede Zone ist so konzipiert, dass sie unabhängig arbeitet: Im Falle einer Störung oder eines Wartungsbedarfs an einem bestimmten Punkt kann nur die betroffene Zone angehalten werden, ohne dass der gesamte Prozess beeinträchtigt wird. Jede dieser Zonen wird von einer AHU (Air Handling Unit) versorgt, die die Arbeitsplätze mit Druckluft versorgt. Alle lokalen RLT-Geräte werden von einem zentralen RLT-Gerät gesteuert, das sich in der Hauptschalttafel befindet und die Luft bei 6 bar konstant filtert und verteilt.
Für den vom Kunden geäußerten Bedarf, der im nächsten Abschnitt beschrieben wird, ist es wichtig zu wissen, dass jede Station durch die folgenden Sicherheitsvorrichtungen geschützt ist:
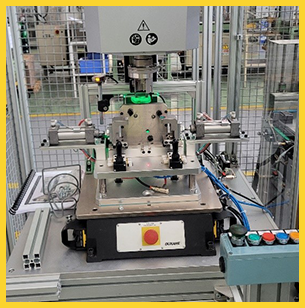
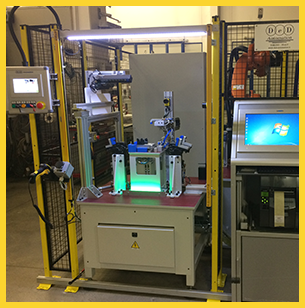
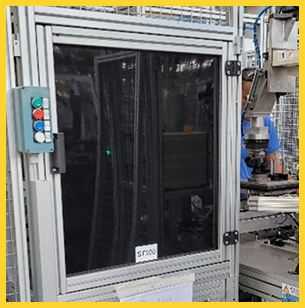
- E-stop: dient der Feststellung des Maschinenstopps (Stopp in Kategorie 0) und der Unterbrechung der pneumatischen Versorgung. Die Rückstellung erfordert den Eingriff des Bedieners;
- Feststehende trennende Schutzeinrichtungen: verhindern den Zugang zu beweglichen Elementen während des normalen Betriebs und zu solchen, die nur gelegentlich für Wartungsarbeiten zugänglich sind. Sie sind mit Schrauben an der Maschinenstruktur befestigt, deren Demontage die Verwendung von Werkzeugen erfordert;
- Bewegliche trennende Schutzeinrichtungen mit Verriegelung: Sie sind mit Scharnieren befestigt und mit Griffen versehen, die ihr Öffnen erleichtern. Sie sind mit elektromagnetischen Mikroschaltern verbunden, die verhindern, dass sie bei laufender Maschine geöffnet werden können;
- Sicherheitslichtvorhänge: Sie schützen gefährliche Bereiche, indem sie eine immaterielle Barriere schaffen, die bei Beginn des Bearbeitungszyklus aktiviert wird und, wenn sie vom Bediener unterbrochen wird, die beweglichen Elemente der Maschine sofort anhält.
Diese Architektur ermöglicht ein selektives und sicheres Management von Ausfallzeiten und Wiederherstellungsmaßnahmen.
Die Sicherheitsanforderungen
Aufgrund der Komplexität und Modularität der Anlage hat DeD die Sicherheitsanforderungen genau definiert:
- Unabhängige Verwaltung der fünf Zonen, ohne Totalstopps bei lokalen Eingriffen;
- Rechtzeitige Steuerung aller Sicherheitsvorrichtungen, einschließlich Nottastern, Mikroschaltern, Verriegelungen, Sicherheitslichtvorhängen;
- ntelligente pneumatische und elektrische Aufteilung für jede Zone, einschließlich elektrischer Achsensteuerung;
- Zukünftige Erweiterbarkeit, mit bereits vorbereiteten Sicherheits-E/A für neue Standorte;
- Optimierung der Verdrahtung und Vereinfachung der Programmierung durch eine zentralisierte Sicherheitsplattform.
Jede Zone benötigt mindestens:
- 4 dedizierte Sicherheitseingänge
- Ausgänge für die Steuerung von STOs, Schranken und Schutzeinrichtungen
- Module für die lokale Signalerfassung und Diagnose
- Ausgänge für die Steuerung von Robotern in Zone 1 und 2
Die ReeR-Lösung: Modulares Sicherheitssystem MOSAIC
Die modulare Plattform MOSAIC von ReeR Safety erwies sich als die ideale Lösung für die Sicherheitsanforderungen des Projekts. Das Herzstück der Sicherheitsarchitektur ist das MOSAIC M1S COM-Modul, das mit folgenden Funktionen ausgestattet ist:
- 8 digitale Eingänge
- OSSD-Ausgänge (2 Paare)
- 4 Testausgänge
- 2 RJ45-Ports für die Kommunikation mit den wichtigsten Feldbussen (EtherCAT, PROFINET, Modbus TCP, Ethernet IP)
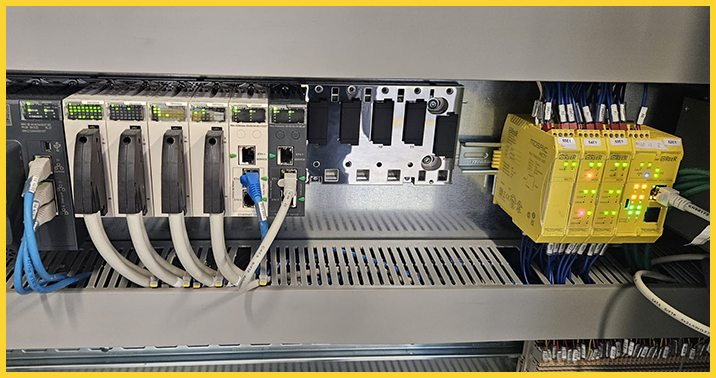
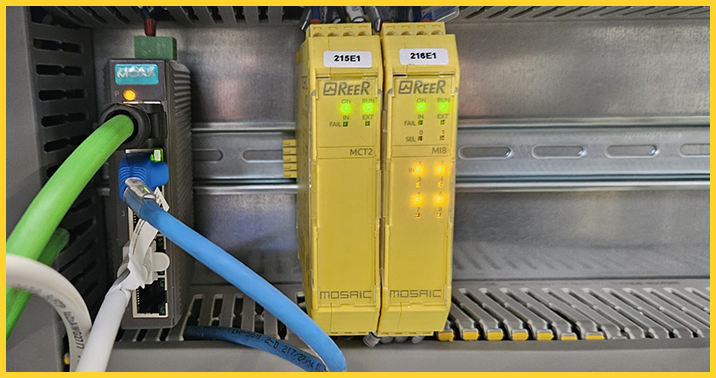
Zusatzmodule für eine verteilte Steuerung
MI16 und MI8: für die Erfassung von Sicherheitssignalen (Nottaster, Schranken, Verriegelungen);
MO4: für die Verwaltung von OSSD-Ausgängen zu Aktoren, Ventilen oder Trennschaltern;
MCT1 und MCT2: für die Fernkommunikation mit lokalen Boxen über MSC-Bus.
Diese Konfiguration ermöglicht eine sichere und unabhängige Verwaltung der einzelnen Zonen. Jede lokale Einheit kommuniziert mit dem Zentralmodul und ermöglicht die selektive Abschaltung einzelner Bereiche und eine rechtzeitige Diagnose. Im Falle eines Eingriffs können die Bediener sicher arbeiten, ohne die gesamte Anlage zu gefährden.
ReeR-Lösung
Sicherheitssteuerungen und -schnittstellen
Mosaic ist ein Sicherheits-Hub, der alle Sicherheitsfunktionen von Maschinen verwalten kann. Es ist konfigurierbar und skalierbar, bietet Kostensenkungen und minimale Verdrahtung.
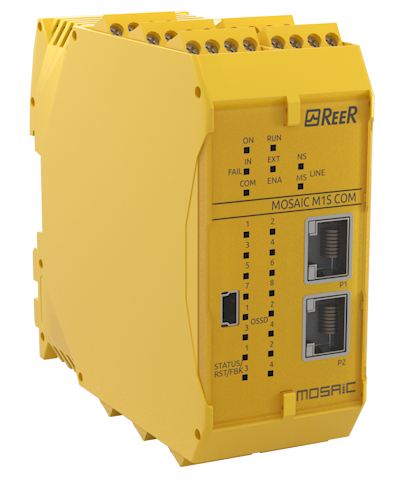
MOSAIC M1S COM
Master-Gerät zur Überwachung jedes weiteren Erweiterungsgeräts, kann auch als Stand-Alone betrieben werden.
- 8 digitale Eingänge
- 4 Eingänge für Anlauf-/Wiederanlaufsperre und EDM
- 4 einzelne OSSD-Sicherheitsausgänge, oder 2 Paare
(PNP 400 mA) - 4 Statusausgänge (PNP 100 mA)
- 4 Testausgänge (zur Kurzschlussüberwachung)
- Integrierter Feldbus Inteface. Protokolle: Ethernet IP, EtherCAT, PROFINET, Modbus TCP
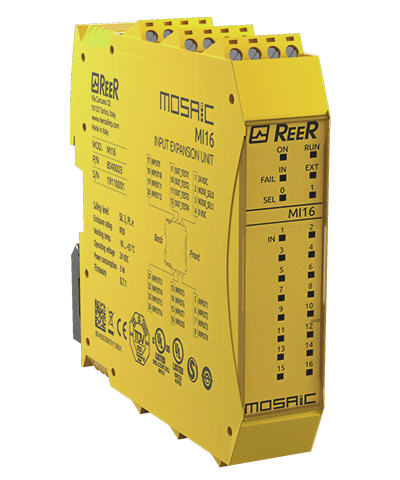
MOSAIC MI8 – MI16
Zusätzliche Eingabeeinheit
- MI8: 8 Digitaleingaben und 4 Testausgänge
- MI16: 16 Digitaleingaben und 4 Testausgänge
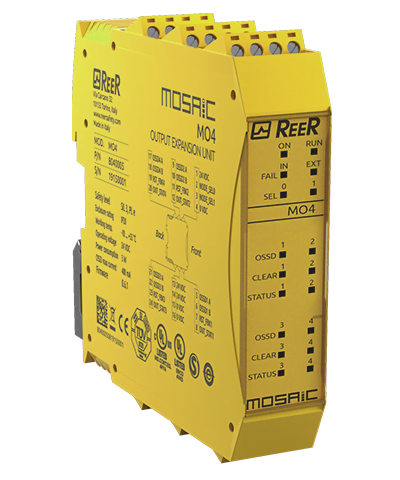
MOSAIC MO4
Ausgangserweiterungseinheit
- 4 einzeln OSSD Sicherheitsausgaben
- 4 Eingaben für Start/Restart Verriegelung und EDM
- 4 Statusausgaben
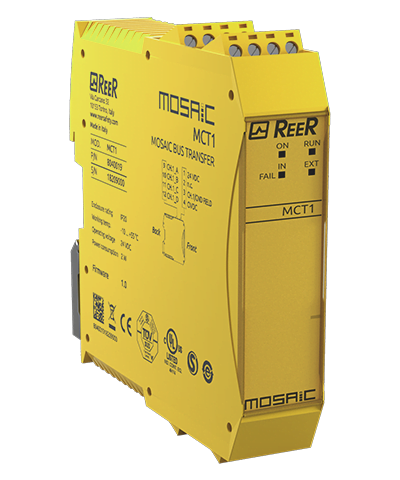
MOSAIC MCT1 – MCT2
Schnittstelleneinheit für den Anschluss von dezentralen Erweiterungen über den MSC-Bus
- MCT1: 1 Anschlussschnittstelle (1 I/O)
- MCT2: 2 Anschlussschnittstellen (2 I/O)
Erzielte Vorteile
Die Einführung der MOSAIC-Plattform hat konkrete und messbare Vorteile gebracht:
- Modularität und Skalierbarkeit: einfache Erweiterung der Linie mit neuen Stationen oder Sensoren;
- Verkürzung der Verkabelungs- und Installationszeiten: dank der dezentralen Struktur;
- Verteiltes Sicherheitsmanagement: jede Zone arbeitet autonom;
- Erweiterte Diagnose und vereinfachte Wartung mit der kostenlosen MSD-Software, die auch Simulation und Designvalidierung ermöglicht;
- Hohe Anlagenverfügbarkeit: Ausfallzeiten werden lokalisiert und minimiert;
- Standardisierung und Vereinfachung: Einheitlichkeit der Komponenten und größere Effizienz bei der Ersatzteilverwaltung.
Eine solide Partnerschaft für sichere Automatisierung
Dieses Projekt ist ein gutes Beispiel dafür, wie die Synergie zwischen einem erfahrenen Integrator wie DeD Automation und einem führenden Anbieter von Sicherheitslösungen wie ReeR zu sicheren, effizienten und zukunftssicheren Anlagen führen kann.
Das Vertrauen, das die beiden Unternehmen verbindet, ist das Ergebnis jahrelanger Zusammenarbeit und gemeinsamer Erfolge. Das MOSAIC-System wurde bereits in zahlreichen Anwendungen eingesetzt, von einfachen Zählern als Einzellösung bis hin zu komplexeren automatisierten Linien wie der gerade beschriebenen zur Herstellung von Thermostatgehäusen. Dank seiner Flexibilität und Zuverlässigkeit ist es die natürliche Wahl für jeden Produktionskontext, der kompromisslose Sicherheit erfordert.
Wenn auch Sie eine automatisierte Linie planen und intelligente, flexible und skalierbare Sicherheitslösungen integrieren möchten, wenden Sie sich an die Experten von ReeR.
Wir sind bereit, Sie in eine neue Ära der sicheren Automatisierung zu begleiten.
ReeR, your future’s safe!